Understanding Friction Modifiers: A Comprehensive Guide
Engine oil friction modifier are essential additives used in lubricants and fuels to enhance performance by reducing friction and wear between moving surfaces. They play a crucial role in the automotive, industrial, and aerospace sectors, where efficient lubrication is vital for the longevity and smooth operation of machinery. This article delves into the intricacies of friction modifiers, exploring their types, mechanisms, applications, and benefits.
what is friction modifier?
Friction modifiers, also known as friction reducers, are chemical compounds added to lubricants to alter the coefficient of friction between two surfaces. They are designed to improve the lubrication performance by reducing friction, wear, and energy consumption. This, in turn, leads to enhanced fuel efficiency, reduced emissions, and prolonged equipment life.
Types of Friction Modifiers
Friction modifiers can be broadly categorized into organic and inorganic types. Each type has its unique properties and applications.
Organic Friction Modifiers
Molybdenum Disulfide (MoS2): This is one of the most widely used friction modifiers. It forms a solid lubricating film on metal surfaces, reducing friction and wear.
Zinc Dialkyldithiophosphate (ZDDP): Commonly used in engine oils, ZDDP provides anti-wear and anti-oxidation properties, extending the life of the engine components.
Esters: Esters are organic compounds that provide excellent lubricity and thermal stability. They are often used in synthetic lubricants.
Fatty Acids: Fatty acids, such as oleic acid, are used to reduce friction in low-temperature applications. They are commonly found in biodegradable lubricants.
Inorganic Friction Modifiers
Graphite: Graphite is a crystalline form of carbon that provides excellent lubrication properties. It is used in high-temperature applications where other lubricants might fail.
Boron Compounds: Boron-based friction modifiers, such as boric acid, offer significant anti-wear and extreme pressure properties.
Ceramic Particles: These are used in high-performance applications to provide superior wear protection and thermal stability.
Mechanism of Action
Friction modifiers work by forming a thin, protective film on the surfaces in contact. This film can be either physical or chemical in nature, depending on the type of friction modifier used.
Physical Film Formation
Inorganic friction modifiers like graphite and MoS2 form a solid lubricating layer that physically separates the contact surfaces. This reduces direct metal-to-metal contact, thereby lowering friction and wear.
Chemical Film Formation
Organic friction modifiers, such as ZDDP, form a chemical film through a reaction with the metal surfaces. This reaction creates a boundary layer that provides anti-wear protection and reduces friction.
Applications of Friction Modifiers
Friction modifier additive are used across various industries to enhance the performance and longevity of machinery. Some common applications include:
Automotive Industry
Engine Oils: Friction modifiers are crucial in engine oils to reduce friction between moving parts, enhancing fuel efficiency and reducing wear.
Transmission Fluids: They improve the smooth operation of transmission systems by reducing friction and wear.
Gear Oils: In gear systems, friction modifiers help in reducing wear and improving the longevity of the gears.
Industrial Sector
Hydraulic Fluids: They enhance the efficiency and lifespan of hydraulic systems by reducing friction between the moving parts.
Metalworking Fluids: Friction modifiers are used in cutting and grinding operations to reduce wear and improve surface finish.
Greases: In industrial applications, greases containing friction modifiers provide long-lasting lubrication under extreme conditions.
Aerospace Industry
Aviation Lubricants: Friction modifiers are used in aviation lubricants to ensure the smooth operation of aircraft components under extreme conditions.
Space Exploration: In space applications, friction modifiers help in reducing wear and ensuring the reliability of critical components.
Benefits of Using Friction Modifiers
The use of friction modifier in engine oil offers numerous benefits, including:
Enhanced Fuel Efficiency
By reducing friction between moving parts, friction modifiers contribute to improved fuel efficiency. This is particularly important in the automotive industry, where reducing fuel consumption and emissions is a key goal.
Prolonged Equipment Life
Friction modifiers reduce wear and tear on machinery, leading to longer equipment life and reduced maintenance costs. This is beneficial across all industries, from automotive to industrial and aerospace.
Improved Performance
In high-performance applications, such as racing or aerospace, friction modifiers help in achieving optimal performance by reducing friction and wear.
Environmental Benefits
The use of friction modifiers can lead to reduced emissions and improved energy efficiency, contributing to environmental sustainability. Biodegradable friction modifiers, such as esters and fatty acids, offer additional environmental benefits.
Challenges and Considerations
Best friction modifier offer significant benefits, there are challenges and considerations to keep in mind.
Compatibility
It is essential to ensure that friction modifiers are compatible with the base lubricants and other additives. Incompatibility can lead to reduced performance or even damage to the machinery.
Cost
Some high-performance friction modifiers, such as ceramic particles and boron compounds, can be expensive. The cost-benefit analysis should be conducted to determine their feasibility for specific applications.
Additive Interactions
Friction modifiers may interact with other additives in the lubricant, potentially affecting their performance. Proper formulation and testing are necessary to ensure optimal performance.
Future Trends in Friction Modifiers
The field of friction modifiers is continuously evolving, with ongoing research and development aimed at improving their performance and expanding their applications.
Nanotechnology
Nanotechnology is playing a significant role in the development of new friction modifiers. Nano-sized particles, such as nano-diamonds and carbon nanotubes, offer superior lubrication properties and wear resistance.
Green Lubricants
There is a growing focus on developing environmentally friendly friction modifiers. Biodegradable and renewable materials are being explored to reduce the environmental impact of lubricants.
Advanced Testing Methods
Advanced testing methods, such as tribological testing and surface analysis, are being used to better understand the mechanisms of friction modifiers and improve their performance.
Innovations in Friction Modifiers
The landscape of friction modifiers is continuously evolving, driven by advancements in science and technology. Innovations are not only aimed at enhancing the effectiveness of friction modifiers but also at addressing environmental concerns and expanding their application scope.
Development of Nanoparticle-Based Friction Modifiers
Nanoparticles are at the forefront of modern lubricant technology due to their unique properties. These particles, often smaller than 100 nanometers, can penetrate and form protective layers on surfaces at a molecular level. Some promising nanoparticle-based friction modifiers include:
Nano-Diamonds: Known for their hardness and thermal conductivity, nano-diamonds reduce friction and wear significantly. They are used in high-performance applications where conventional lubricants might fail.
Carbon Nanotubes (CNTs): CNTs exhibit excellent mechanical properties and can form a strong, durable film on surfaces. They are particularly useful in extreme conditions where high pressure and temperature are prevalent.
Metallic Nanoparticles: Metals like silver, copper, and gold, when used as nanoparticles, provide superior lubrication and wear resistance. They are especially effective in applications requiring high thermal stability.
Final Thoughts
Friction modifier additives are essential additives that play a crucial role in enhancing the performance and longevity of lubricants. Their ability to reduce friction and wear makes them invaluable in various industries, including automotive, industrial, and aerospace. By understanding the types, mechanisms, applications, and benefits of friction modifiers, we can make informed decisions to optimize lubrication performance and achieve better efficiency and sustainability.
Organic friction modifier additives market As technology advances, the development of new and improved friction modifiers will continue to drive innovation in lubrication, leading to more efficient and environmentally friendly solutions. Whether in engines, transmissions, hydraulic systems, or high-performance applications, friction modifiers will remain a key component in the quest for better lubrication and reduced wear.
FAQs

Does Your Car Need High Mileage Oil? (Signs You Should Switch)
Does Your Car Need High Mileage Oil? (Signs You Should Switch) Discover More As vehicles age, their engines undergo significant wear, leading to reduced efficiency and potential breakdowns. One of the most effective ways to maintain an older engine is by switching to high-mileage oil, specially formulated for cars with 75,000 miles or more. But how do you know if your car needs it? What are the key benefits, drawbacks, and alternatives? And why should you consider Ruamnza Xrace Pro Oil for your high-mileage vehicle?

Does Your Diesel Engine Need a Special Oil? (The Truth Revealed)
Does Your Diesel Engine Need a Special Oil? (The Truth Revealed) Discover More When it comes to maintaining a diesel engine, one of the most critical decisions you’ll make is choosing the right oil. Diesel engines operate under extreme conditions—high compression, intense heat, and heavy loads—which means they require a lubricant that can withstand these challenges. But does your diesel engine really need a special oil, or can you use any high-quality motor oil? In this comprehensive guide, we’ll uncover the

What is Anti-Freeze Coolant? Types, Colors & How to Use
What is Anti-Freeze Coolant? Types, Colors & How to Use Discover More Anti-freeze coolant, also known as engine coolant or radiator fluid, is a specially formulated liquid that regulates engine temperature, prevents overheating in summer, and protects against freezing in winter. It is a mixture of water, ethylene glycol or propylene glycol, and chemical additives that enhance engine efficiency and longevity. Without proper coolant, engines can suffer from: Overheating (leading to warped cylinder heads or blown gaskets) Freezing (causing cracked engine blocks in cold climates) Corrosion (damaging radiators,
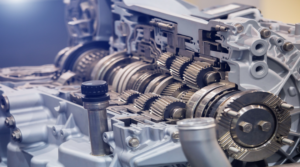
What is ATF? Types of Transmission Fluid & When to Change It
What is ATF? Types of Transmission Fluid & When to Change It Discover More Transmission fluid is one of the most critical yet often overlooked components in a vehicle’s maintenance routine. Whether you drive an automatic, manual, continuously variable transmission (CVT), or dual-clutch transmission (DCT) vehicle, the right transmission fluid ensures smooth operation, longevity, and peak performance. What is Automatic Transmission Fluid (ATF)? Automatic Transmission Fluid (ATF) is a specialized lubricant designed to reduce friction, cool transmission components, and facilitate smooth
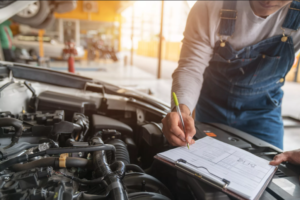
Fuel Injector Cleaner: Does It Really Work? (Analysis, Benefits, and Top Picks)
Fuel Injector Cleaner: Does It Really Work? (In-Depth Analysis, Benefits, and Top Picks) Discover More Modern engines rely on precise fuel delivery to maintain performance, efficiency, and emissions compliance. Fuel injectors play a critical role in this process by atomizing fuel into a fine mist for optimal combustion. However, over time, carbon deposits, varnish, and contaminants can clog injectors, leading to poor engine performance. Fuel injector cleaners are chemical additives designed to dissolve these deposits and restore injector efficiency. But do they
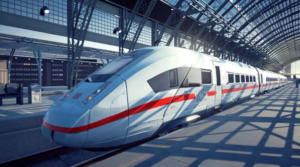
Best Railroad Engine Oils in 2025 – Boost Performance & Longevity
Best Railroad Engine Oils in 2025 – Boost Performance & Longevity Discover More The railroad industry is a backbone of global logistics, transporting millions of tons of cargo and passengers daily. Given the immense stress on locomotive engines, selecting the best railroad engine oil is crucial for optimal performance, fuel efficiency, and engine longevity. In 2025, advancements in lubrication technology have led to high-performance synthetic blends, low-ash formulations, and smart additives that enhance engine protection under extreme conditions. This guide
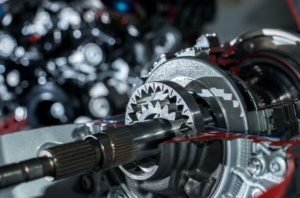
Best Transmission Treatments to Extend Your Vehicle’s Lifespan (2025 Guide)
Best Transmission Treatments to Extend Your Vehicle’s Lifespan Discover More Maintaining your vehicle’s transmission is crucial for ensuring longevity, smooth performance, and fuel efficiency. With advancements in automotive technology, transmission treatments have evolved significantly in 2025. This guide explores the best transmission treatments available, their benefits, and how they can help extend your vehicle’s lifespan. Understanding Transmission Systems and Their Importance A vehicle’s transmission is responsible for transferring power from the engine to the wheels, enabling smooth gear shifts and